Solutions
-
Building Automation Systems
Reduce energy costs, personnel costs, equipment failures & unnecessary service calls with a state-of-the-art building automation system upgrade. Automate control of & integrate your HVAC, lighting, & security systems.
-
Lighting Control Systems
TMBA engineers, technicians, and programmers are seasoned experts at developing and implementing an appropriate Lighting Control System strategy for your building or facility.
-
Integrated Security Systems
Today’s security threats, along with more stringent compliance codes & standards, highlight the need for more comprehensive and integrated security solutions. We can help.
About TMBA
T.M. Bier & Associates was established in 1977 in Long Island, NY. Since that time, the company has grown into the metropolitan New York area’s most prominent independent automated building management systems engineering company.
The design & installation of HVAC systems, lighting controls systems, security systems & various industrial controls is only part of the solution that we provide to our clients.
We use the most advanced technology on the market in the design, installation, monitoring & service of HVAC systems & controls, lighting controls, security systems & various industrial controls.
Our Projects
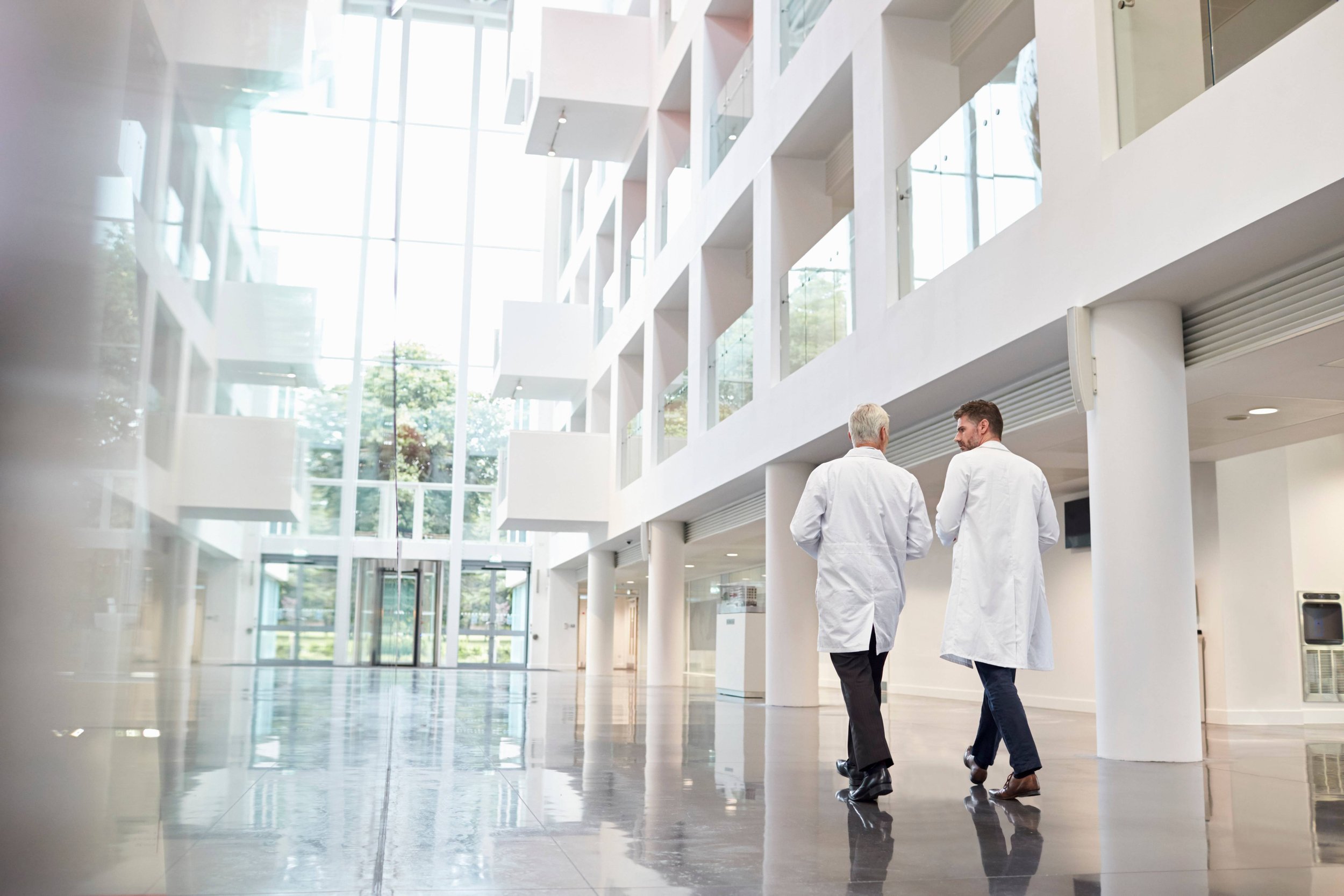
Dedicated To Your Success
We build long term commitments with our customers through courteous, trustworthy, and knowledgeable service. The team from TMBA shares a common goal, to earn your complete satisfaction on every job.
Testimonials
Read The Latest From Our Blog…
Our Partners